How Load Matching Creates Energy Savings and Lowers Costs
Matching plant operation to actual equipment demand creates significant energy and cost savings.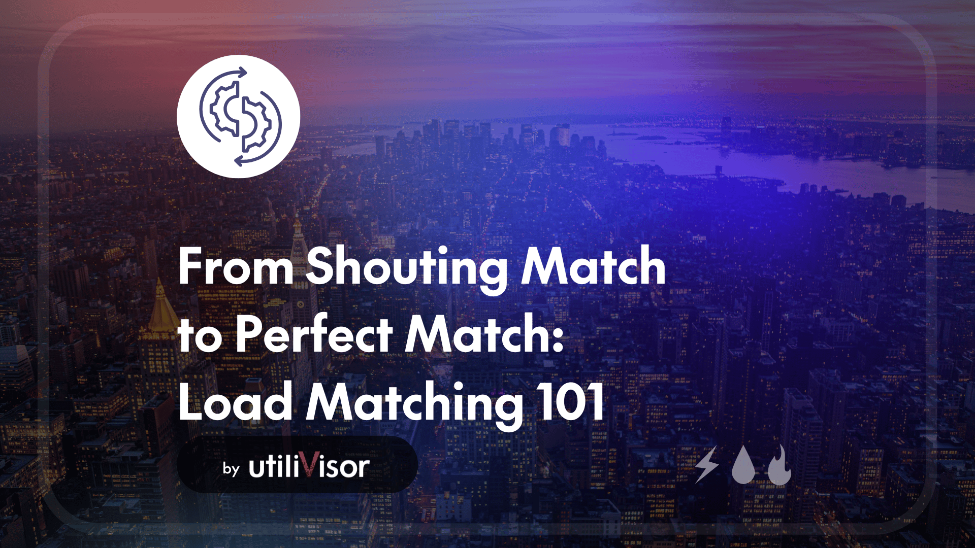
We’re not normally in the relationship business. But we think it’s time everybody broke up with high energy costs. Like your ex, your load is demanding too much.
So think of this as an intervention. The good news is that this intervention puts money back in your pocket. We're talking real, documented, site-wide savings of 8%–15%.
How exactly can we achieve that, you ask?
Load matching. Think of it as couples counseling for your plant and your equipment but without the awkwardness (or the judgment).
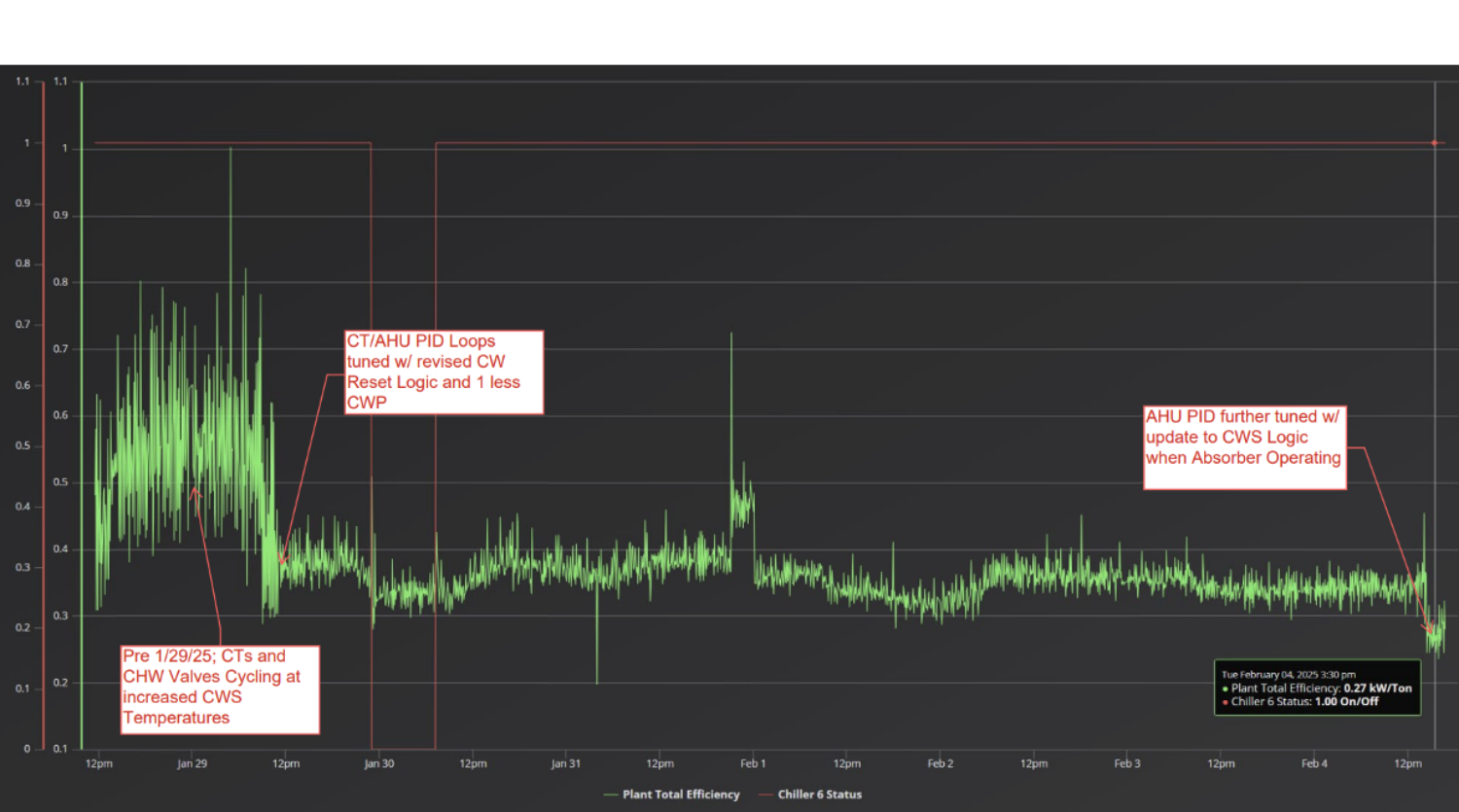
What Is Load Matching?
Load matching is the process of balancing the equipment to the load to meet requirements. For example, how much steam or AC is needed to keep room temperatures within range? Which equipment is needed to produce that amount, and what conditions would affect what to stage on and when?
The goal of load matching is to smooth out the operations throughout the entire operational system. This ends up being an iterative process because you want to provide the bare minimum of power or tonnage or whatever is called for to satisfy the system. But that also means you need to make sure that you’re not calling for more than you need. So on the plant side, you don’t want to overdeliver, and on the field side, you don’t want to “overdemand.” Instead, we look to find that happy medium. What’s the smallest amount of energy or highest air or water temp we can deliver that satisfies the needed conditions for each area/space serviced?
Typically we start load matching in the central chiller plant. We identify what adjustments are needed to optimize the performance of the plant equipment so they use less energy. The question we're trying to answer is this: How can we deliver load with the lowest possible energy usage, given the equipment on the system and the demand profile?
After we’ve worked in the central plant, we’ll move on, usually to the air handling units. We go through the same process for each unit, asking, Are set points satisfied? Can they be adjusted to reduce energy? Is scheduling on so the unit turns off at night, or is the AC running even when no one is around and nothing else is happening?
Then, we move out to the next level in the system. For example, is the need for chilled water now low enough that we can use fewer chillers or pumps and still meet the desired conditions? We try to understand how the parts work together and which parts or settings have an outsized impact on the system as a whole.
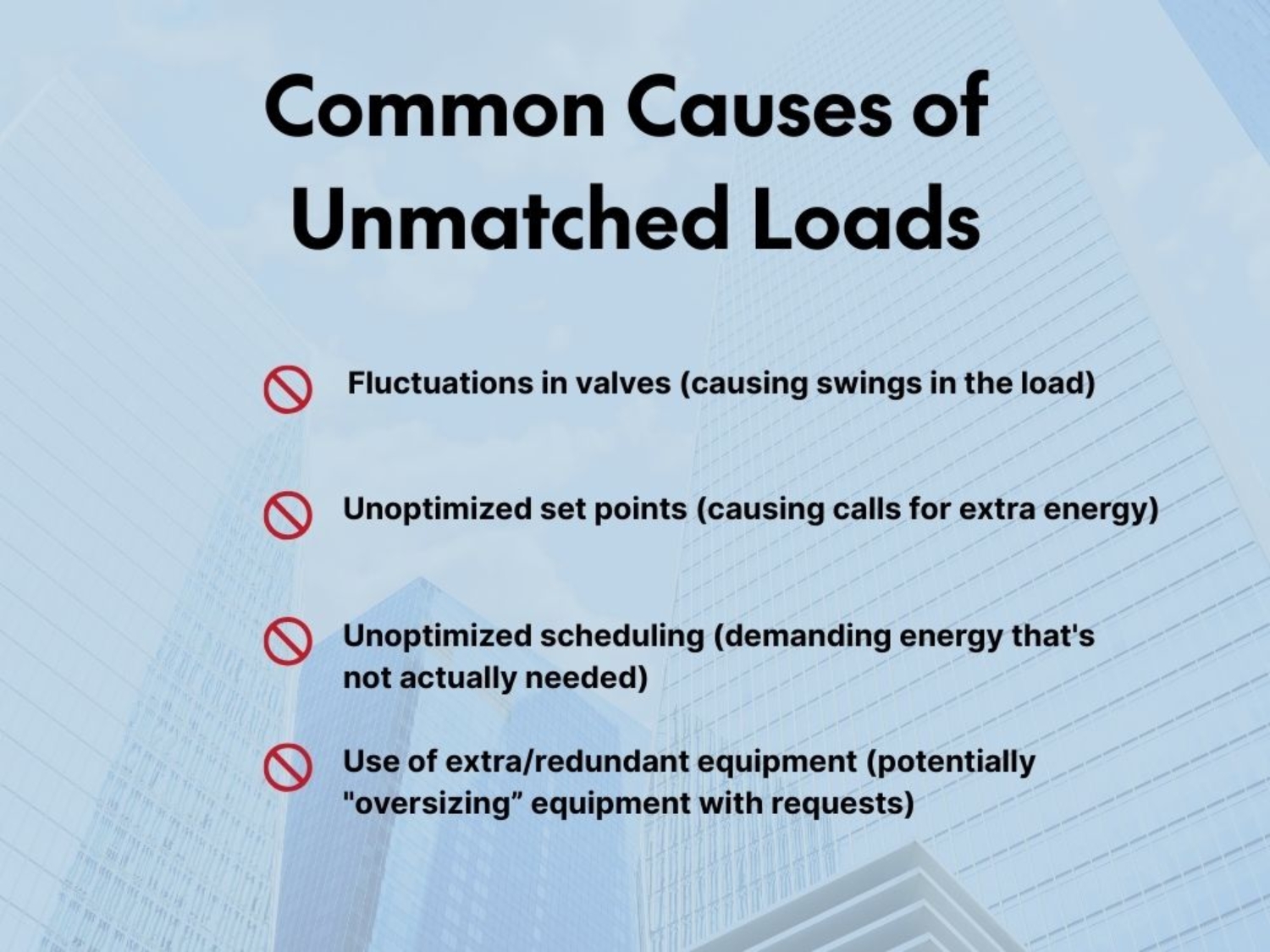
When Is It Worth Running Redundant Equipment?
Some sites choose to regularly operate more equipment than they need. They know they rarely have to use both chillers to keep the offices cool enough. But they also know that they’re going to get complaints if the temp goes up even a smidge, so they run the extra chiller to avoid issues. And we get it – It gets hot by 3 or 4 pm in the summer.
But the energy and cost trade-off here can be significant. What if you stage that second chiller on at 3:30 or 4:15 pm, yet everyone in the building goes home at 5 pm? How much is that hour or so of extra chiller costing you versus going over that max temperature by only half a degree most days?
We can’t say whether it’s worth it to you to operate redundant equipment vs. open a discussion with tenants about afternoon cooling and energy bills. But we can put dollars to exactly how much that margin of “safety” is costing you so you know exactly what your trade-offs are.
A Quick Case Study on Load Matching
A hospital client asked us for load matching last year. The table below lists some of the savings we found, just by syncing the load with the equipment, with no impact on medical equipment requirements or patient comfort.
Quick Takeaways on Load Matching
1. Save significantly without compromising comfort.
As our hospital case study shows, load matching can drive site-wide savings of 8%–15% while maintaining temp and other operational requirements.
2. A systematic approach yields holistic understanding.
Successful load matching requires understanding how a change in one area impacts others. A comprehensive approach helps prevent unintended consequences while maximizing efficiency gains.
3. Find the balance between redundancy and efficiency.
While operating redundant equipment is a safe approach to maintaining comfort, it often has serious cost implications. Understanding those energy costs helps to resolve strategy dilemmas by putting solid numbers to trade-offs.
You Might Like
About utiliVisor
Your tenant submetering and energy plant optimization services are an essential part of your operation. You deserve personalized energy insights from a team that knows buildings from the inside out, applies IoT technology and is energized by providing you with accurate data and energy optimization insights. When you need experience, expertise, and service, you need utiliVisor on your side, delivering consistent energy and cost-saving strategies to you. What more can our 45+ years of experience and historical data do for you? Call utiliVisor at 212-260-4800 or visit utilivisor.com